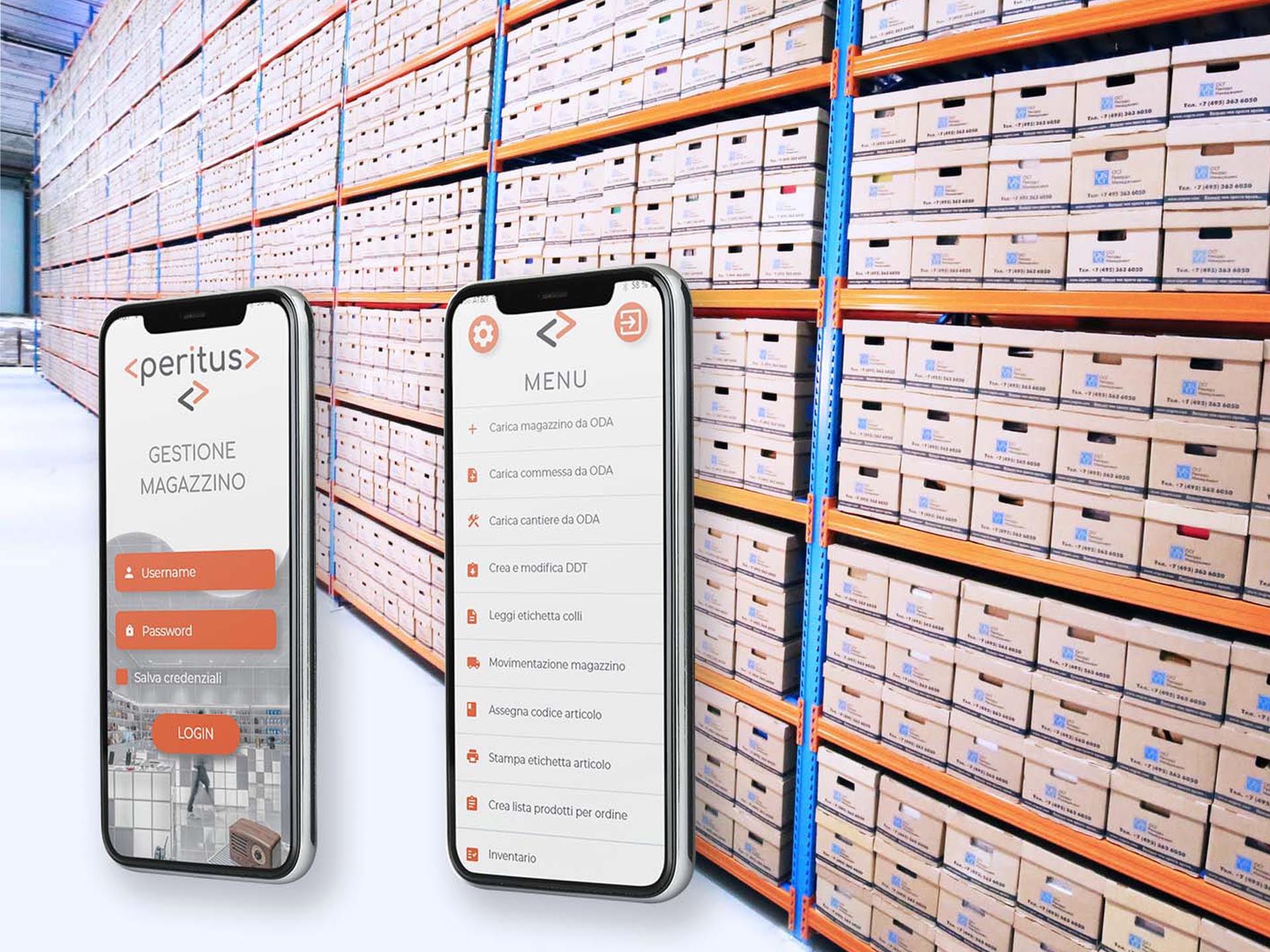
Warehouse management app: the case history of RG Impianti
The problem
The correct management of a warehouse must respond to a coordinated system based on precise business objectives. Each action performed in the warehouse must leave a trace to be linked with the accompanying documentation of the goods. How many times do you have surplus stocks, instead? How often are they in short supply or are they even out of stock? How often do inaccuracies occur in product registration and handling?
All of these problems involve significant waste of time and money. The risk: to fail delivery times and leave unsatisfied customers behind.
The digital solution
Peritus developed an app offering a digital approach to the management of processes closely related to the material world. The electronic exchange of data and the scanning of the barcodes of all the warehouse items minimize any errors and / or inaccuracies. The working conditions of the employees are also significantly simplified.
The tailor made app has been developed to meet the management needs of RG Impianti, a company from Northeastern Italy specialized in plant engineering for the civil and industrial field. It is a mobile app for Android phones and tablets for warehouse management by internal staff, who access the system via profiling. The database resides on a client’s own server.
Solutions to problems: the app
We developed the RG app to implement the efficiency and accuracy of logistics operations inside and outside the warehouse. It is a management software that dematerializes most of the documentation and logistics operations: from the data entry relating to transport documents to stocks and inventory, from the management of loading / unloading of items to reporting on the movement of goods, up to the alerts upon reaching of the minimum stocks set by the system or on the fixed goods. The software therefore returns a precise and updated overview of the stock of goods available and the position occupied within the warehouse, facilitating the planning and management of orders. The app then provides a feature for scanning item barcodes and printing labels via airprint.
Implementations in progress
As a tailor-made product, we adapted the app to the new requests that emerged during the development phase. Work order management (ODL) is now in progress, as well as that of a semi-finished page that can always be modified during the material preparation. It can be created from scratch or from an order and can be printed on a label with a distinctive sign. This is a draft of what DDT will be in effect. The management of return notes and material rental is also being implemented.